MAG Welding Defined
Aug 20, 2018
Automating your MAG welding process will help to bring faster and more consistent cycle times. A robotic MAG welder will also help to improve the weld quality, helping your customer's become more satisfied with the final product. If you are interested in integrating a new or refurbished robotic system, contact Robots.com experts today.
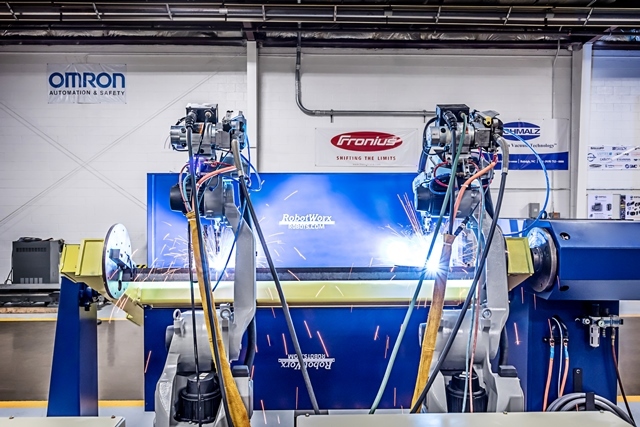
MAG welding robots are the perfect contender for welding processes where the quality and speed of the repetitive weld are crucial. It’s a great way to improve efficiency and consistency while quickly receiving a Return On Your Investment.
Metal Active Gas (MAG) automated Welding is similar to MIG welding, yet differs in the type of shielding gas used. They are both sub types of welding method classified as GMAS (gas metal arc welding). However, MIG uses Metal Inert Gas while MAG uses Metal Active Gas.
The heat for the welding process is created by a DC electric arc that helps to fuse the consumable metal electrode to the piece that is being worked on. This metal electrode (a small diameter wire) is fed by powered feed rolls (wire feeder) and becomes part of the weld pool. Both the arc and the weld pool are shielded by a chemically active gas. An active gas is in the protective gas category of M21, also known as mixed gas 18 or MIX 18. These gases meant to shield, also react during welding and can affect the seam surface, metallurgy, penetration, behavior, arc stability, and droplet transition. This gas is discharged to help prevent the molten metal beneath the arc from oxidizing.
If necessary, the compositions of gas can be mixed up and changed for the welding process to actively affect and adapt to the right material. Typically, MAG is used for steel and MIG for nonferrous metals.
There are three metal transfer modes that can be used, depending on the operating features necessary, for the process. Short-circuiting and pulsed metal transfer are perfect for low current operations. Short-circuiting (“dip transfer”) has the molten metal form on the tip of a wire and is transferred by the wire dipping into the weld pool. Spray transfer is used during high welding currents. This technique must use higher voltage to make sure the wire doesn’t make contact with the weld pool. The molten metal on the tip of the wire transfers to the weld pool in the form of a spray of small droplets (smaller than the diameter of the wire). These droplets are then detached randomly across the arc by applying pulses of currents. The pulsed mode was developed as a means of stabilizing the open arc below the threshold, to avoid spattering and short-circuiting.
After better understanding the MAG process, it is easy to see the advantages to automating this process step. A big advantage of MAG welding is the ability to easily integrate reconditioned refurbished robots for this application. These robots can save you up to 50% on cost, without sacrificing performance quality.
Robots.com has over 25+ years of integrating welding robots, especially MAG and MIG welding robots. All of our pre-owned robots go through a rigorous reconditioning process which restores the refurbished robot to like-new conditions and extends its life comparable to a new robot.
Robotic welding automation includes faster, consistent cycle times, no break in production, and overall better weld quality. Robotic weld cells are also available and can enhance production flow and increase worker safety.
Interested in automating a MAG operation with an industrial robot? Contact us by filling out this form, or call us at 877−762−6881 to start building your MAG welding robot solution today.
Related Articles
You might be also interested in:
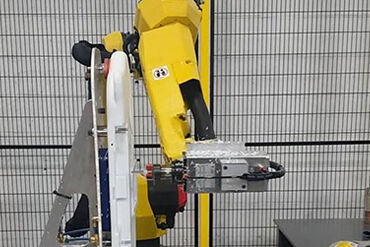
- Featured
Latest Advancements in Material Cutting Robotics
Read about the latest technological advancements in robotic material cutting.
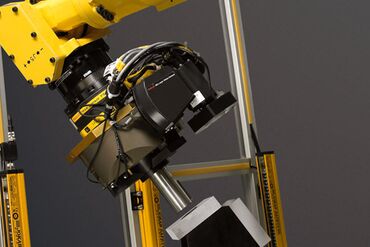
- Featured
Emerging 3D Vision Technologies for Industrial Robots
Learn about the emerging 3D vision technology that businesses are using for industrial robot applications.
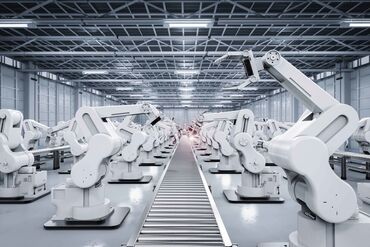
- Featured
Most Popular Industrial Robotic Applications for 2021 and Projections
Explore the most popular application trends of 2021 and what to expect in the future.
Let's talk!
Request your quick quote today.